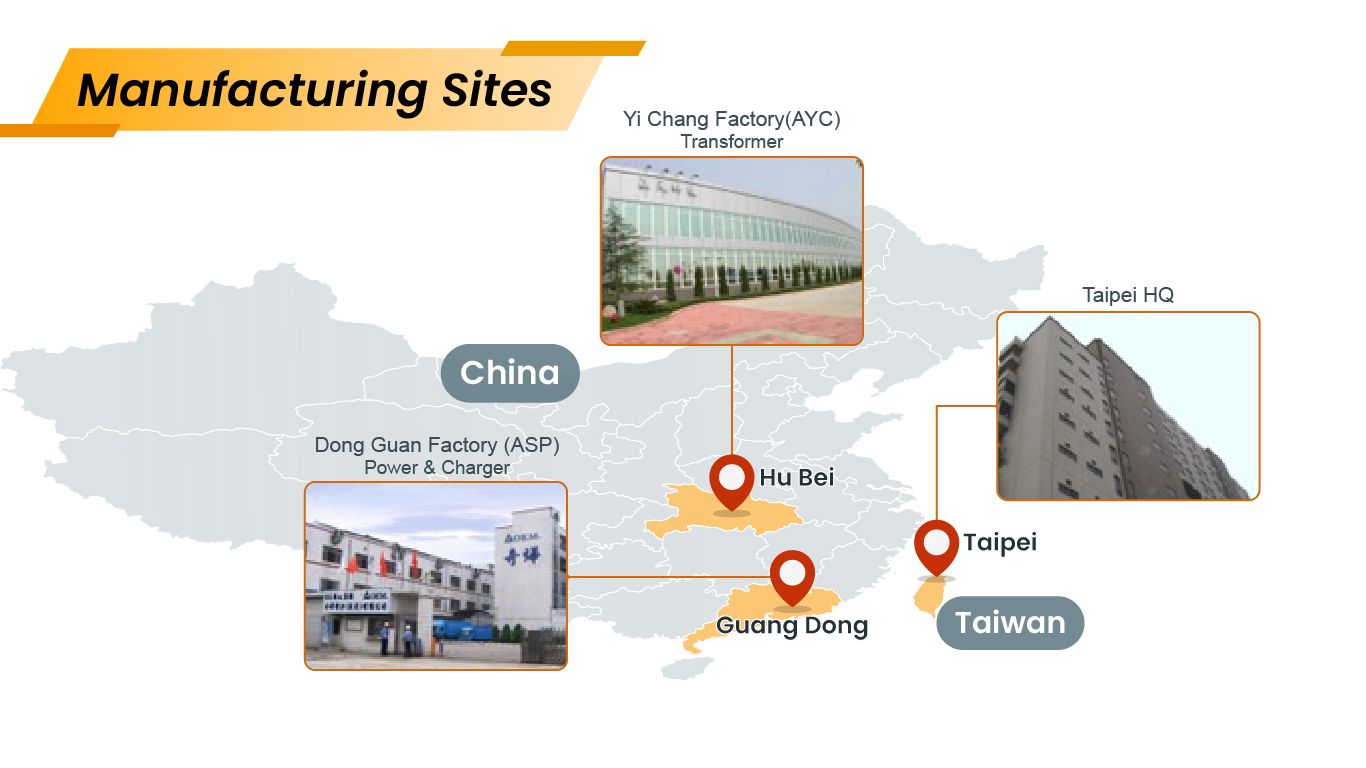
Production Ability
QQE: Leading the Charge in Smart Lithium/Lead acid Battery Charger Technology
Welcome to QQE, located in the advanced manufacturing hub of Shipai Town, Dongguan City, China! We are one of the leading manufacturers of smart battery chargers, committed to innovation and excellence.
•Production Capacity:
•Two highly efficient production lines.
•Monthly capacity of up to 52,000 chargers in per production line.
•Total production capacity of an astounding 104,000 units.
Our manufacturing craftsmanship and technological expertise ensure outstanding product quality. Whether for home use or commercial applications, QQE smart battery chargers undergo rigorous testing and quality control to ensure safety and reliability.
Through continuous innovation and technological advancement, QQE is dedicated to driving the development of smart battery charger technology to meet the ever-growing demands of customers. Whether you are seeking the latest in smart charging technology or a reliable partner, QQE is here to fulfill your needs.Join QQE and let's pave the way for a smarter charging future together!
QQE: Comprehensive Smart Battery Charger Production Process
At QQE, we manufacture smart battery chargers using the most advanced production processes to ensure that each product meets the highest quality standards. Here's an overview of our production process:
1.SMD Placement: Precisely place components onto PCB using Surface Mount Device (SMD) technology.
2.AI Sub-Automatic Insertion: Automate the accurate insertion of components onto the board, enhancing production efficiency.
3.Manual Insertion (MI): Components are manually inspected and inserted to ensure correct installation.
4.Wave Soldering: Pass the assembled PCBs through an automatic wave soldering machine for soldering.
5.Touch-up: Professional technicians conduct necessary manual solder touch-ups to ensure solder joint quality.
6.AOI (Automated Optical Inspection): Utilize automated optical inspection systems to check solder joints and component placement for quality assurance.
7.Pre-Test: Conduct preliminary electrical characteristic tests to check basic functionality.
8.Assembly: Assemble various components together to complete charger assembly.
9.Burn-in Test: Subject chargers to extended operational testing to ensure stability and reliability.
10.2nd Test: Perform a second round of electrical characteristic testing to verify all functions.
11.Ultrasonic Welding: Seal the enclosure and internal components securely using ultrasonic welding technology.
12.Hi-Pot Testing: Conduct high-voltage testing to ensure chargers meet safety standards.
13.Final Test ATE (Automated Tester - Chroma 8000): Utilize automated testing equipment for final comprehensive testing to verify charger performance and quality.
14.Labeling (Laser): Laser-mark relevant information and labels onto the charger.
15.Final Inspection: Conduct a final visual inspection to ensure product appearance is flawless.
16.Packaging: Use automated packaging systems to package chargers for shipment.
17.At QQE, we uphold a spirit of continuous improvement in every production stage to deliver the highest-quality products to our customers
18.I hope this meets your needs! Let me know if you need any further adjustments or modifications.